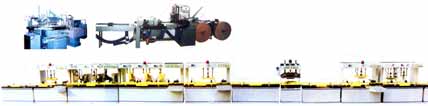
FLEXIBLE:The same line can produce the whole range
of automotive batteries, both with in-line and traverse connections,
from 160 to 520 mm of length (this includes all the current European,
American and Japanese standard sizes. 36Ah¨¤200Ah)
MATCHED TO YOUR NEEDS: you
can have just he automation level and the production rate that suit
your needs. The different options available span from semi-automatic
systems to computer-controlled lines capable of producing 4 batteries
per minute and operated by one man. .
RELIABLE: During
the assembling process the batteries undergo a series of accurate
tests, automatically carried out, for short circuit detection, check
of the intercell weldings and heat sealing leakage detection. These
tests, added to the precision and quality of VOLT
operation units, give the assurance of the quality of the final
product-all the batteries coming out from the line comply with the
standards set by you.
COMPACT:all the VOLT
assembly line are engineered for making the best use of your floor
space.
our
offer is only a half of that from Wirtz, TBS, ¡, one sixth
of that from SOVEMA, but their performance is never poor. Specially,
our COS and enveloping machine & stacker are strong competitive
against TBS and SOVEMA
FULLY AUTOMATIC VOLT ASSEMBLY LINE, Line SM-4
The
Fully Automatic VOLT Assembly Lines incorporate into an integrated
system all the operations for the final assembly of PP batteries.
Before the line, it is only necessary that the punched containers,
plates and separators, are stored in a continuous row, then the
conveying system transfers them one by one to the following operating
units, where the arrival, clamping, working cycle and release of
the battery are carried out on an automatic sequence.
Enveloping and stacking station-
Specially envelop the plates with the PE separator and stack
the group from 2~41 plates at the same time ensure the higher output
and constant quality. The enveloping machine for PE and stacking
machine for leaf separators, e.g. PVC, HR, are available separately.
Cast-On-Strap/COS Station-
for efficient production of high quality cos connections, This machine
is very flexible in operation being able to accommodate SLI batteries
of 6¡Á1, 3¡Á1& 3¡Á2 layout. Automation COS production
can be accomplished on this single machine with the aim of rotary
design and up-down motion, manually turn-over, semi-auto-align and
auto-polish the lugs, advanced PC unit and program-control. The
production practice have well proved the COS(cast-on-strap) machine
not only meets the processing requirements, commercially produces
quality plate groups, but also has achieved internationally advanced
level of the same kind.
The group is inserted into the containers by manual.
Short Circuit/Group Inversion Detection
Station- the VOLT test system checks on a programmed
eequence the cells; if any short circuit is detected, an alarm is
given and the battery is automatically sent to the rejection conveyor.
The test parameters, such as voltage and acceptable range of leakage
current, are adjustable to suit the different battery types and ambient
conditions. An optional group inversion test equipment can be fitted
to this station. Test electrodes with adjustable position dispense
with the need of interchangeable tool plates.
Connectors- The VOLT
Fully Automatic Welding Machine, Type IWM-4, specially designed for
all current types of SLI batteries, with 6x1, 3x2 or NATO cell layout,
brings you the latest technology into through-partition welding of
inter-cell connections, specially designed three heads for higher
outputs (up to 4 batteries per minute). Cycle and positioning
movement are controlled by an electronic axis-control unit. The unit
can store the programs for 99 different type of battery. the data
are stored in EPROMs, which ensure their integrity even in the event
of a power shutdown. Cycle movements are precisely actuated by encoder-controlled
direct current motors, with a repeatable position accuracy of 0.1mm.
This machine features an innovative micro-processor welding control
system, which ensures welds of constant quality. The system is adaptive,
in that it automatically offsets the small differences in welding
conditions between one battery and the next. When, however, the weld
parameters reach values which can not be offset any further, or which
exceed the specified acceptance range, an extremely sensitive surveillance
system interrupts the cycle, sounds an alarm and sends the battery
to the reject conveyor. The control is performed during the welding
process and is therefore certainly more selective than after-welding
checks: mechanical tests, which cause stress on the connection, are
no longer required in the assembly line.
Current & Shear Testing Station Specially designed for testing
the welding checks of thru-partition for all current types of SLI
batteries, with 6x1, 3x2 or NATO cell layout, specially three heads
for higher outputs (up to 4 batteries per minute). Highly automatic,accurate and rapidly, programmable shear and heavy currenttesting
HEAT
SEALING STATION-
Accurate
temperature and pressure control assures an uniform quality of
the sealing. The machine is pneumatically operated and is produced
in two version: standard, with heating element 600x300mm, and
enlarged, which can either heat-seal two batteries at a time up
to 330mm long, or a single one up to 800mm.
Pressure
Testing Station-
The
tightness of the sealed junction is tested by applying an air
pressure and detecting the leakage between adjacent cells or towards
the outside. Test duration and pressure are adjustable; when the
leak exceeds the pre-set threshold the rejection of the battery
is automatic. Also this station features an adjustable test head,
eliminating any need of tool replacement.
Post-burning Machine Number Printing
and Aluminum Foil Sealing - it is fully automatic
to print the 10-digital numbers ( for date, series number, ¡)
on the bodies of batteries by heating. The uminum foil will be covered
on the vents against the moisture through heat welding at the same
time.Enveloping and stacking station can also be separated to supply(called
Line-3) depends on the customer¡¯ requirements.SEMI-AUTOMATIC
VOLT ASSEMBLY LINE, Line SM-3, 3+, HR-3 For all those manufactures
who do not require a high production output or need aq side production
line for small series, , we have also developed a simplified version
of its assembling equipment, incorporating the same basic technology
but based on idle rollers and manually operated stations.
These lines offer the same high quality of the automatic ones combined
with the maximum flexibility; the output is proportional to the number
of operators engaged (from three to seven) and
the change over of the
tools is as simplified as possible. Specially,
Line HR-3 is designed for assembling the hard rubber batteries. This
line includes rotated welding station, stacking station, bridge connecting
and gel stabilizing station. Its capacity is up to 300 batteries per
shift.
Rotated welding station:
Here made the plates groups. The plates will be welded to form the
groups with half-post and terminals. The small parts will be produced
separately by manual or die casting.
Stacking station:
Here made the cells. The welded group and
separators are inserted in order. While inserting, their quality is
also checked.
Bridge connecting and gel stabilizing station:
Here made completed batteries. The cells be connected by bridges,
the lids will be sealed by gel. The
parts and raw materials are transported to the suitable positions
automatically. Note:
Line SM-4, fully assembly line for PP batteries.
SM-3, SM-3+, semi-automatic assembly line for PP batteries.
HR-3, semi-automatic Hard Rubber assembly line for HR batteries. |